News
Engineers Discover Greener Industrial Chemical Production Method Led by Tulane
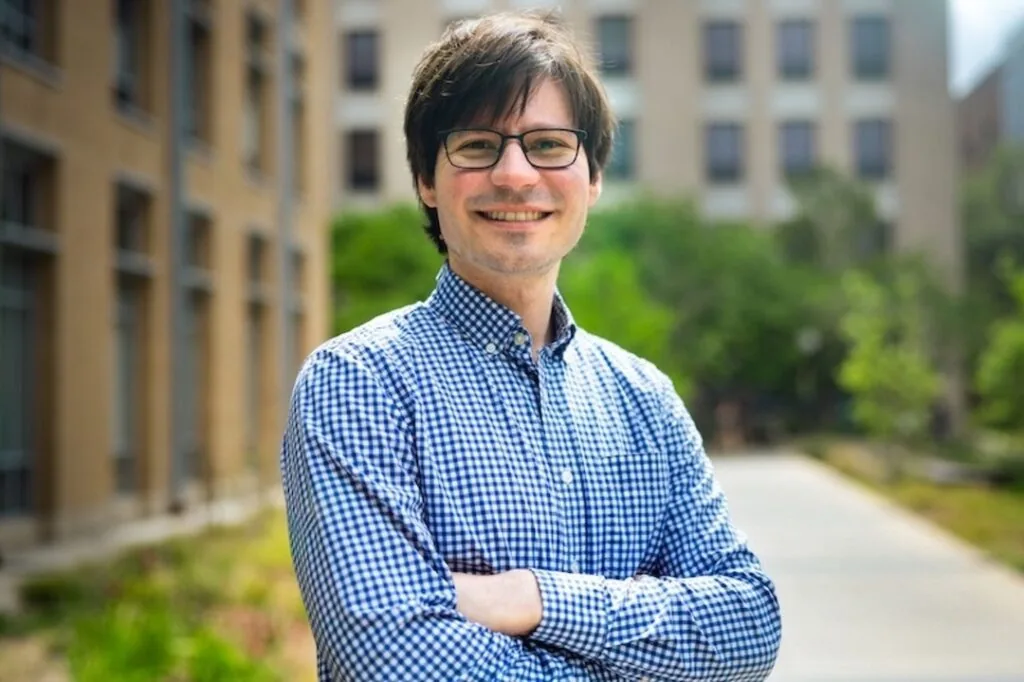
NEW ORLEANS (press release) – Scientists at Tulane University have discovered a potentially greener way to produce a crucial industrial chemical used to make many everyday products from plastics and textiles to antifreeze and disinfectants. According to a new study in Science, the prominent science research journal published by the American Association for the Advancement of Science (AAAS), the breakthrough could significantly reduce greenhouse gas emissions from the manufacture of ethylene oxide.
The study, “Nickel promotes selective ethylene epoxidation on silver,” co-authored by Tulane University chemical engineer Matthew Montemore, has the potential to transform the manufacture of ethylene oxide, which has an estimated $40 billion global market value.
The current ethylene oxide production process requires chlorine, which is toxic and emits millions of tons of carbon dioxide into the atmosphere annually.
“If industry does try this out and they find it to be useful and are able to commercialize it, the twin benefits are you can save a lot of CO2 and a lot of money at the same time,” Montemore said.
Getting rid of toxic chlorine could also make production safer, Montemore added.
The discovery was six years in the making. Sykes and Montemore first discussed exploring selective oxidation reactions in 2018. They focused on ethylene oxide production, which converts ethylene and molecular oxygen using silver as the primary catalyst.
“We were surprised because we couldn’t find anything in the scientific or patent literature about nickel despite it being a common and inexpensive element used in many other catalytic processes,” Sykes said.
The breakthrough came through applying Sykes’ single-atom alloy concept, a fundamental approach to understanding and controlling chemical reactions that he pioneered over a decade ago. Montemore thought this approach could be applied to oxidation reactions, even though Sykes had not had much success with oxidation in the past.
The team then enlisted Christopher, an expert on catalytic reactor studies, to develop a practical formulation of the silver catalyst with nickel additions.
The results exceeded expectations.
Anika Jalil, a doctoral student at UCSB successfully developed a reproducible method for incorporating nickel atoms into the silver catalyst, a technical challenge that may explain why this effect had never been previously reported.
The current industrial process for producing ethylene oxide typically generates two molecules of carbon dioxide per ethylene oxide molecule. Adding chlorine improves this ratio to about two molecules of ethylene oxide per carbon dioxide molecule. The new nickel-enhanced catalyst could potentially reduce these emissions further.
The team has submitted international patents for its discovery and is in discussions with a major commercial producer about implementing the technology in existing manufacturing facilities.
If successful, this cleaner production method could help address the significant environmental impact of ethylene oxide manufacturing while maintaining the efficiency needed for industrial-scale production.